Pick and pack errors
Increasing productivity levels is important in any industry, but especially in a fast-paced environment such as a warehouse. Picking and packing errors in warehouses create inefficient work environments that waste time and money. At Mappedin, we have some tips on how to reduce picking and packing errors and maintain a speedy pick and pack execution without compromising accuracy. Let’s start by explaining the different methods warehouses use to pick and pack.
Picking methods
Zone picking
Zone picking, also known as the pick and pass method, divides the warehouse into separate zones. Each picker will be given a specific section and will then pass the product to the next employee working in their designated zone. This promotes continual picking, allowing employees to ship orders at a quicker rate. Zone picking allows each employee to focus solely on a specific area, including the equipment required in their section. This minimizes training requirements, for instance, not everyone will need to learn how to operate a forklift if it is not required in their zone. Zone picking can promote a smooth workflow for order picking by minimizing crowds and eliminating congestion.
Batch picking
Batch picking, or “multi-order picking,” requires a picker to combine orders by SKU. This enables multiple orders to be picked at once as businesses can pull large amounts of inventory together by fulfilling big batches of items at one time. This creates a greater optimization of picking shifts with one order schedule window for each shift. Batch picking reduces travel time in a warehouse by fulfilling multiple orders at once and encourages high levels of productivity when order picking.
Wave picking
Wave picking is when an order is picked one SKU at a time. This method organizes orders into windows that are then scheduled to be picked at certain times throughout the day. This allows for full control over the timing of order picking which positively impacts the flow of products. Wave picking can be used simultaneously with zone or batch picking, for example, waves can be allocated at various times to separate zones.
Now that we have identified these picking and packing methods, let’s dive into some tools that can minimize picking errors when utilizing zone, batch, and wave picking.
1. Indoor navigation systems
Indoor maps
A warehouse relies on flow, accessibility, and space to operate smoothly. In a fast-paced environment, it is crucial that the layout of the warehouse promotes an effective and productive work environment. When planning the layout of a warehouse, it is important to ensure that items of importance are placed in the most ideal locations and equipment is properly stored. Instead of manually moving around items and equipment in a warehouse, a company can use digital indoor maps to plan their layout accordingly. 3D digital maps allow warehouses to try different layouts and see which is the most suitable for their venue. Design your warehouse based on your goals, whether it be changing the layout to increase efficiency for pickers or optimizing the layout for inventory receiving. Digitally planning layouts with a 3D indoor map can reduce pick and pack mistakes by minimizing areas or congestion and optimizing product locations.
Indoor wayfinding
A warehouse needs to have an efficient and optimized pathing system to save wasted travel time for employees while meeting all safety requirements. After the creation of a 3D map, indoor wayfinding can be implemented within the map to create optimal pathing for warehouse employees. This increases the productive workflow between picking and packing orders or receiving and shipping inventory. With an indoor wayfinding system for warehouses, employees can reduce pick and pack errors by following optimal routes while picking and packing, whether that be passing orders to a different zone or finding a product an employee is looking for.
Employees can also gain information about amenities on the map such as equipment. The 3D map can provide information about equipment protocols and training required to operate a machine while also notifying an employee of its availability status. With the implementation of blue dot technology into indoor navigation systems, warehouses can see the exact indoor location of employees on the map and which routes they are taking. This can enable warehouse managers to assess which areas can be improved while also avoiding overstaffing by seeing how crowded optimal paths are. Employees can create a picklist on the 3D map and use wayfinding to see the optimal route to follow when collecting the items they need to fulfil an order.
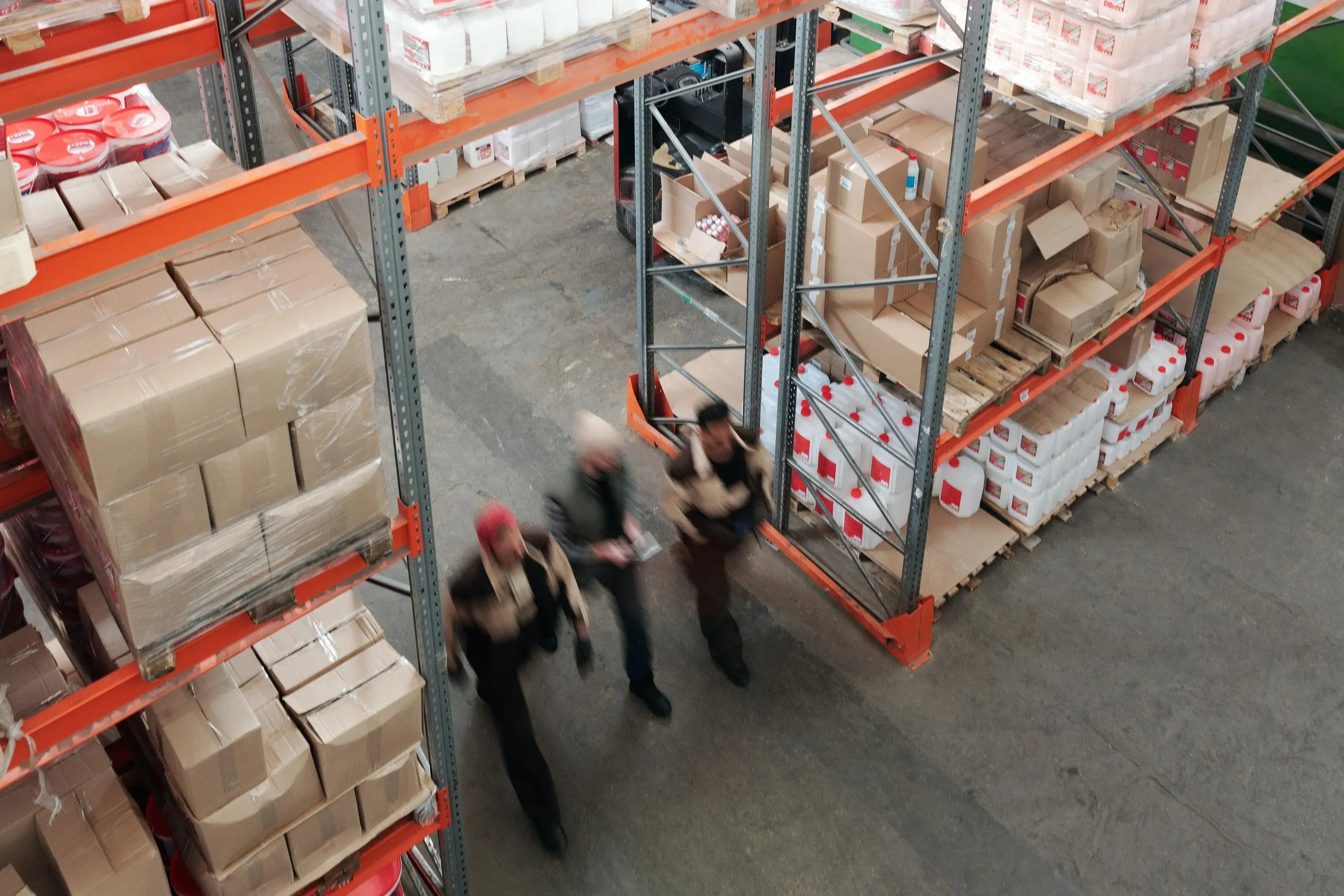
2. Asset tracking
It is easy for items and equipment to get misplaced when moving through a warehouse. Indoor positioning systems can be used for tracking assets in the building. Warehouses can tag equipment to view its location on an indoor map in real-time. This can account for anything from large pieces of machinery to tiny storage bins. With asset tracking, employees can save time searching for assets by seeing exact locations of equipment on the map in real-time. Asset tracking can promote accountability when knowing who is responsible for what. Asset tracking can also help minimize congestion by seeing which equipment is being used where and if there is a more efficient way to assign equipment based on the spacing of the venue and the preferred method of picking and packing.
3. RFID technology
Radio Frequency Identification (RFID) technology is composed of tags and readers. The tags use radio waves to communicate their identity and other information to readers, which are devices that emit radio waves and receive signals from the RFID tag. RFID tags can store information from one serial number to several pages of data, keeping important information all in one place.
Inventory management
Manually keeping a count of items can be mentally draining on employees and promotes picking errors. RFID systems eliminate paper usage and improve inventory accuracy by tracking warehouse production and counts in real-time. This technology creates a wireless workflow that relays information about the status of an item, eliminating the manual labour of scanning barcodes to see an item’s status update. This minimizes mistakes that can occur when picking and shipping multiple orders by allowing RFIDs to automatically identify and track items in a warehouse and manage inventory counts accordingly.
Meeting regulations
RFID scanners also ensure government regulations are met when dealing with products like food and pharmaceuticals. Properly adhering to government regulations is crucial when ensuring products are manufactured with consumer health and safety in mind. When meeting regulations, a company can reduce the risk of receiving fines and penalties due to negligent errors. RFID tags can automate regulation procedures from monitoring equipment to ensure safety or reporting on an item's production status to see how, where, and when a product was created.
Safety & security
Automate safety and security measures with RFID tags to reduce stress when scrambling to ensure safety procedures are being met. RFID tags can wirelessly verify users and machines to ensure only authorized individuals can operate equipment or enter a particular area. This can enable warehouses to avoid using passwords and implement RFID authentication to make security an easy and stress-free experience.
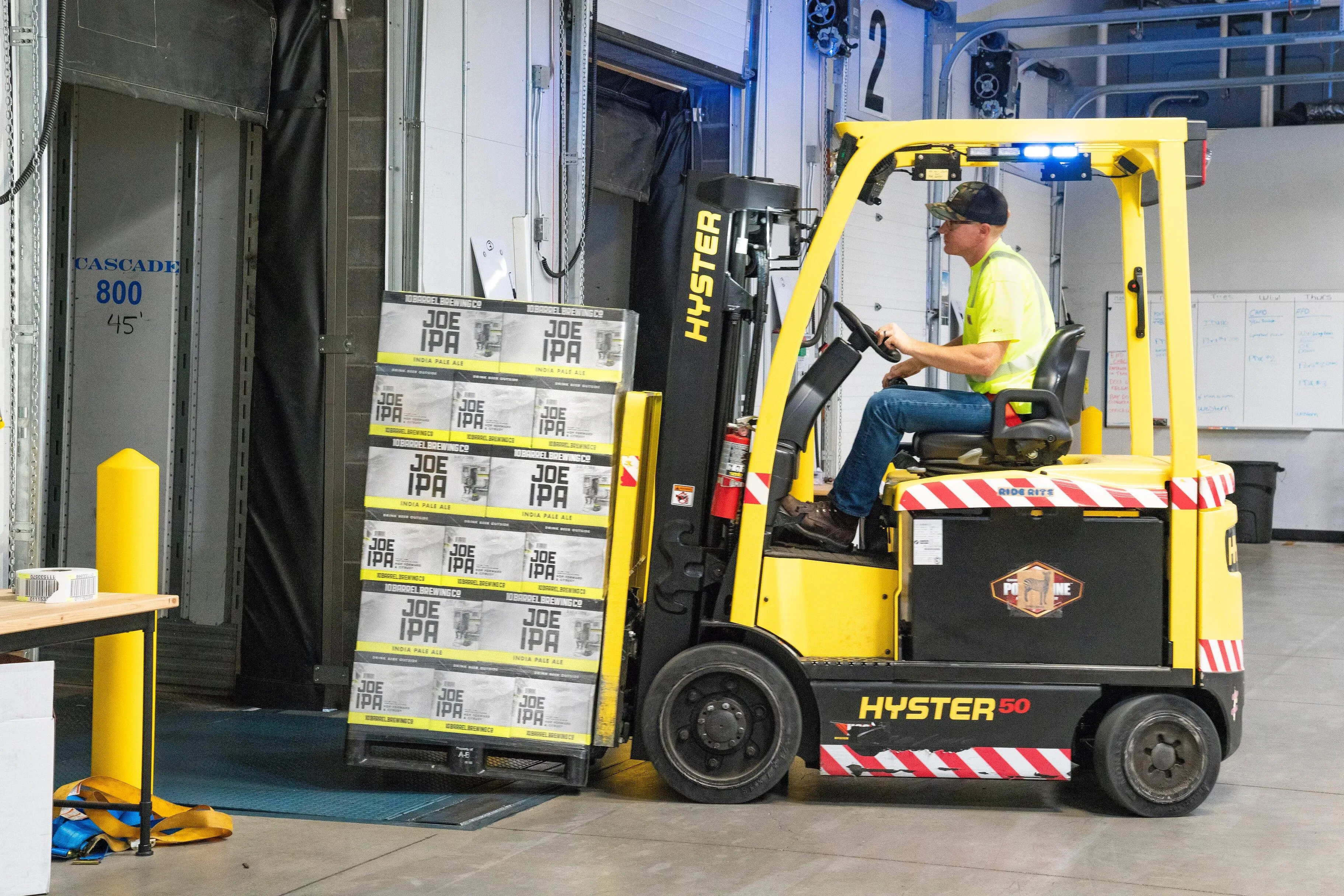
4. Barcode technology
Barcode technology can assign locations to specific items, such as a specific bin, shelf, or stock room to reduce picking errors. Barcodes allow a business to keep on top of their inventory by clearly displaying an item’s location within a warehouse to avoid workers grabbing the wrong items. Barcodes eliminate the manual process of using paper-based systems, which can be time-consuming and prone to human error. Barcode technology can allow a warehouse team to be more accurate and productive when picking and shipping items.
Automated barcode labelling
When working in a warehouse, fatigue, disengagement and stress can cause human errors like miss-picking items with similar ID tags, mistakenly mislabelling an item with the wrong SKU number. It is easy for errors like this to occur when working quickly and following picking methods that use sequential SKU numbers. Barcode labelling technologies eliminate the task of reprinting and relabelling products, which can put a strain on labour, budget, and increase unnecessary manual labour. A printed order can get lost easily, making the pick and pack process difficult and time-consuming. Automated barcode labelling systems can reduce error by avoiding misspelling and misheard information about an item. Automated labelling systems use distinct and unique SKUs that can increase organization and minimize picking errors like grabbing a wrong item, making employees’ lives easier.
Barcode scanners
Barcode scanners can ensure barcode labels are accurate to verify each item that is picked. These scanners validate each order by seeing if the item matches the SKU so pickers and packers can do their job without error and a business can reduce strain on labour budgets. Scanners can save time and money when reducing picking mistakes. Barcode scanners keep all product information in one digital place to increase organization in warehouses. Barcodes can also enable data insights and analytics for inventory tracking when integrated with inventory automation systems, asset tracking, and other third-party solutions.
5. Mobile robots
Picking and packing productivity can be greatly improved in warehouses when implementing mobile robots. Mobile robots can work around the clock and recharge when needed to reduce physical and mental strain on a picker and packer that can lead to error. Mobile robots can follow optimized routes created from wayfinding technology. This eliminates unnecessary walking so employees can focus their time accordingly and increase efficiency.
Amazon is an example of a warehouse that currently uses over 100,000 mobile robots to create a productive work environment. These robots decrease the time needed to manually retrieve items from storage bins, shelves, and stock areas by half. The robots operate in a gated area separate from the employees and bring storage units to the workers for the pick and pack process. These robots carry shelves of products from worker to worker by reading barcodes on the ground to get directions on which path to take. Mobile robots perform tedious tasks that allow employees to easily identify items when picking and packing rather than finding them on shelves or in storage bins.
6. Half-picked order procedures
Depending on which picking and packing method a company chooses, sometimes employees will pick part of an order and have it ready for when the rest of the items arrive. This process can get complicated and cause mistakes when keeping tabs on fulfilled orders and half-picked orders. Technologies like inventory software systems can help identify half-picked orders and keep track of them. There also needs to be space allocated for these orders so items don’t get lost if someone were mistakenly to put items from a half-picked order back on the shelf. A company can limit the number of times half-picked orders occur to prevent mistakes and order errors while keeping a count of inventory levels. This can result in splitting an order into separate shipments to avoid delays on complete order. Measures must be put in place to reduce pick and pack errors on half-picked orders to maintain a reliable business.
7. Warehouse management systems
Warehouses are utilizing many upcoming technologies as they have a large workflow to keep track of and all of the amenities listed above can be difficult to monitor when implementing separate technologies. A warehouse management system can keep track of all information in one central location. They can also be used to see what is working and what can be improved through insights and analytics. Insights and analytics can be used to track employees’ routes in wayfinding systems, asset tracking paths, mobile robot paths, barcode accuracy and more. A warehouse team can use this platform to see which items are of most importance and place fast-moving products in optimal locations. They can also monitor the location of storage bins, barcode scanners, inventory checks and more. Pickers and packers can benefit from these platforms by operating in an organized warehouse. Warehouse software systems can implement physical signs around the warehouse that correspond with 3D digital map smart labels, to ensure pickers and packers are directed at all times.
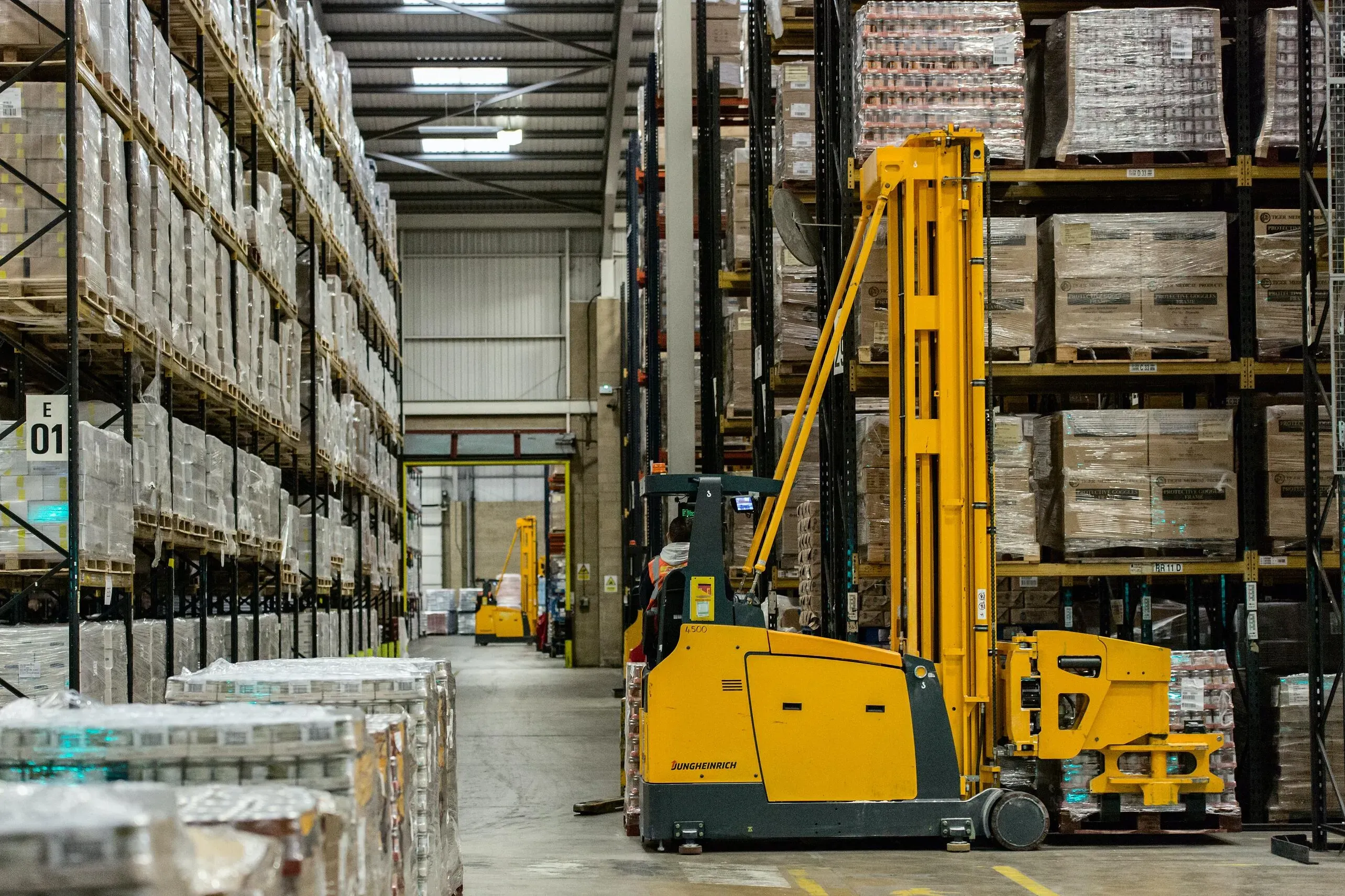
Pickers and packers move quickly around a warehouse. With these tips, picking and packing can become a seamless process with minimal errors. Contact us or visit our website to start reducing errors in your warehouse.
Tagged In
Share